Machines as Mathematical Functions: A New Perspective on Optimization
This piece explores how machines can be analyzed using mathematical functions—addition, subtraction, and multiplication—to enhance efficiency, troubleshooting, and design. It provides real-world examples, such as multi-cylinder engines, servo motor feedback loops, and gear torque multiplication, to illustrate how machines combine efforts, correct errors, and amplify power. This structured approach helps engineers and facility managers optimize performance and improve reliability in manufacturing and facility operations.
3/27/20254 min read
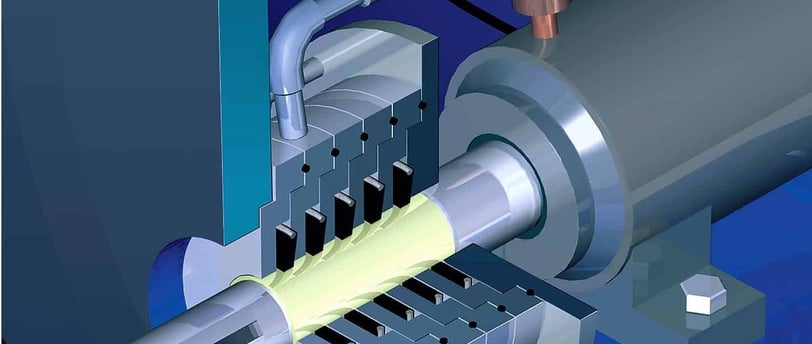
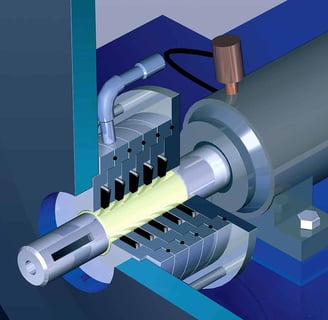
In manufacturing and facility operations, machines are the backbone of productivity. While they are traditionally understood through mechanics and engineering principles, they can also be analyzed through a mathematical lens. By treating machines as sets of functions—similar to mathematical operations such as addition, subtraction, and multiplication—we can develop a deeper understanding of how they work.
This approach provides a structured way to optimize efficiency, diagnose issues, and improve machine design. Facility managers, engineers, and manufacturing professionals can use this framework to break down complex machinery into manageable components, making troubleshooting and performance analysis more precise and effective.
Machines as a System of Functions
Every machine consists of interconnected parts, each performing a specific role. If we view each part as a function and the machine as the sum of these functions, we can analyze its behavior systematically.
Parts = Functions – Each part performs a transformation, affecting inputs and outputs.
Input = Components – These are the raw materials, energy, or signals entering the system.
Operation = Interconnections – These define how parts interact, whether through mechanical, electrical, or hydraulic means.
Output = Machine Performance – The final transformation that allows the machine to complete a task.
This approach helps categorize how different machine components interact, leading to improved diagnostics, design, and troubleshooting.
Addition of Machine Functions: Combining Efforts
In mathematics, addition means combining multiple elements to create a greater whole. Similarly, machines often integrate multiple components to enhance performance.
Example: Multi-Cylinder Engines
In internal combustion engines, power output is the sum of the contributions of each cylinder. A single-cylinder engine provides limited power, but adding more cylinders increases the total output. This concept applies to large industrial engines used in ships, generators, and high-performance vehicles.
Example: Conveyor Systems in Manufacturing
In automated production lines, conveyor belts are often powered by multiple motors. If one motor fails, the overall system performance drops, but the other motors can compensate. This redundancy increases reliability and efficiency in material handling.
Troubleshooting Applications:
If a machine’s total output is lower than expected, check whether all contributing components are functioning properly.
In multi-motor systems, performance drops may indicate an underperforming motor.
In parallel electrical circuits, a failure in one component can reduce total power—test each function separately.
Machine Design Considerations:
Using multiple components in parallel increases redundancy, reducing the risk of complete failure.
More functional units improve efficiency and flexibility in machine design.
Distributing workload across multiple components extends the lifespan of individual parts and minimizes wear and tear.
Subtraction of Machine Functions: Error Correction & Feedback
Subtraction in mathematics represents the difference between two values. In machines, this concept is applied in control systems and feedback loops, where the difference between actual and desired performance is measured to ensure accuracy.
Example: Servo Motor Error Compensation
Servo motors in robotics and CNC machines use sensors to compare their actual position to the target position. If there is a difference, the motor adjusts to correct the error in real time. This ensures precision in automated manufacturing, where even small misalignments can lead to defects.
Example: HVAC Systems and Temperature Control
Heating, ventilation, and air conditioning (HVAC) systems use thermostats to regulate room temperature. If the actual temperature deviates from the set temperature, the system compensates by adjusting heating or cooling output, maintaining a stable environment.
Troubleshooting Applications:
If a machine is not meeting specifications, compare expected vs. actual performance to identify underperforming components.
In control systems, deviations from expected values indicate an issue—analyze feedback signals to locate the problem.
In temperature control systems, if actual temperature deviates from the setpoint, adjust the regulating function accordingly.
Machine Design Considerations:
Machines should include error detection mechanisms for self-correction.
Feedback loops ensure dynamic adjustments to maintain precision.
Predictive maintenance tools can use this concept to anticipate failures before they occur, reducing downtime.
Multiplication of Machine Functions: Amplification & Power Scaling
Multiplication in mathematics means one function scales another. In machines, this principle applies to amplification, where small inputs create significantly larger outputs.
Example: Gear Torque Multiplication
In gear trains, output torque is determined by gear ratios. A small motor can generate high torque when paired with a gear system, making it possible to move heavy loads with minimal effort. This principle is widely used in industrial machines such as presses, cranes, and conveyor systems.
Example: Hydraulic Systems in Heavy Machinery
Hydraulic systems amplify force by using fluid pressure. A small hydraulic input can generate massive output forces, allowing heavy equipment like bulldozers and forklifts to lift and move large loads efficiently.
Troubleshooting Applications:
If a machine is not producing enough power, check whether the multiplication function (gears, pulleys, hydraulics) is operating correctly.
In manufacturing presses, inconsistent force output may indicate worn-out gears or hydraulic issues.
In pulley systems, improper belt tension can reduce mechanical advantage, leading to inefficiencies.
Machine Design Considerations:
Properly scaled components prevent overload and extend machine lifespan.
Multiplication functions should be optimized to balance power and efficiency.
Regular maintenance of gears, belts, and hydraulic systems ensures consistent performance.
Conclusion
By analyzing machines as mathematical functions, engineers and facility managers can gain valuable insights into system performance, troubleshooting, and design.
Addition principles help optimize efficiency through parallel contributions.
Subtraction principles improve precision through error correction and feedback.
Multiplication principles enhance power and force scaling for improved performance.
This framework provides a structured approach to understanding complex machinery, making it easier to diagnose faults, optimize systems, and enhance reliability in manufacturing and facility operations. Whether designing new equipment, troubleshooting existing systems, or improving efficiency, viewing machines through a mathematical lens can lead to smarter engineering solutions.